360° Approach
For Toyota, producing environmentally-friendly vehicles is one small part of the overall picture. We take a 360° approach to the whole lifecycle of the vehicle, starting from its design all the way through to how it can be recycled at the end of its life.
As part of this approach we believe that they should also be produced in sustainable, environmentally-friendly facilities by people who measure their performance in terms of positive social and environmental impact.
By striving to minimise the resources we consume, reduce the amount of energy, water and substances of concern used, as well as the amount of waste created in the manufacturing process, we are continuously reducing the environmental impact of our operations.
In 1992 Toyota established the “Earth Charter” as part of its Global Policy towards environmental protection. The values and commitments of the charter are reflected as core values within Toyota Motor Manufacturing UK Ltd’s (TMUK) environmental policy. Since the start of production at TMUK these values have helped us to become a class leader in environmentally friendly manufacturing at both of our UK sites.
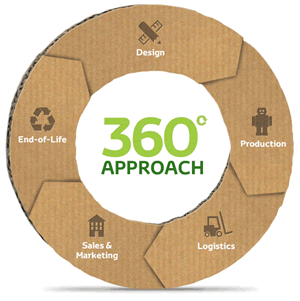
Discover TOYOTA
TMUK Charitable Trust
Through the social contributions programme, over £6.3 million has been donated to charities and organisations by Toyota.
Lean Approach Seminars
Come directly to the source at our Burnaston state of the art manufacturing facility and learn more about Toyota's approach to manufacturing.
TOYOTA Glossary
Find the meaning behind the common terms used by Toyota.
TOYOTA and The Environment
At every stage of a vehicle's life, Toyota strives to protect the environment through reducing energy use and minimising waste.